How Digital Tools Are Transforming Precision Welding in Springfield, MO
Revolutionizing Precision Welding with Digital Tools
The welding industry in Springfield, MO has experienced a remarkable transformation over recent years, primarily due to the integration of digital tools. These advancements have not only improved the quality and precision of welding but have also enhanced efficiency and safety. As more businesses adopt these technologies, the landscape of precision welding continues to evolve.
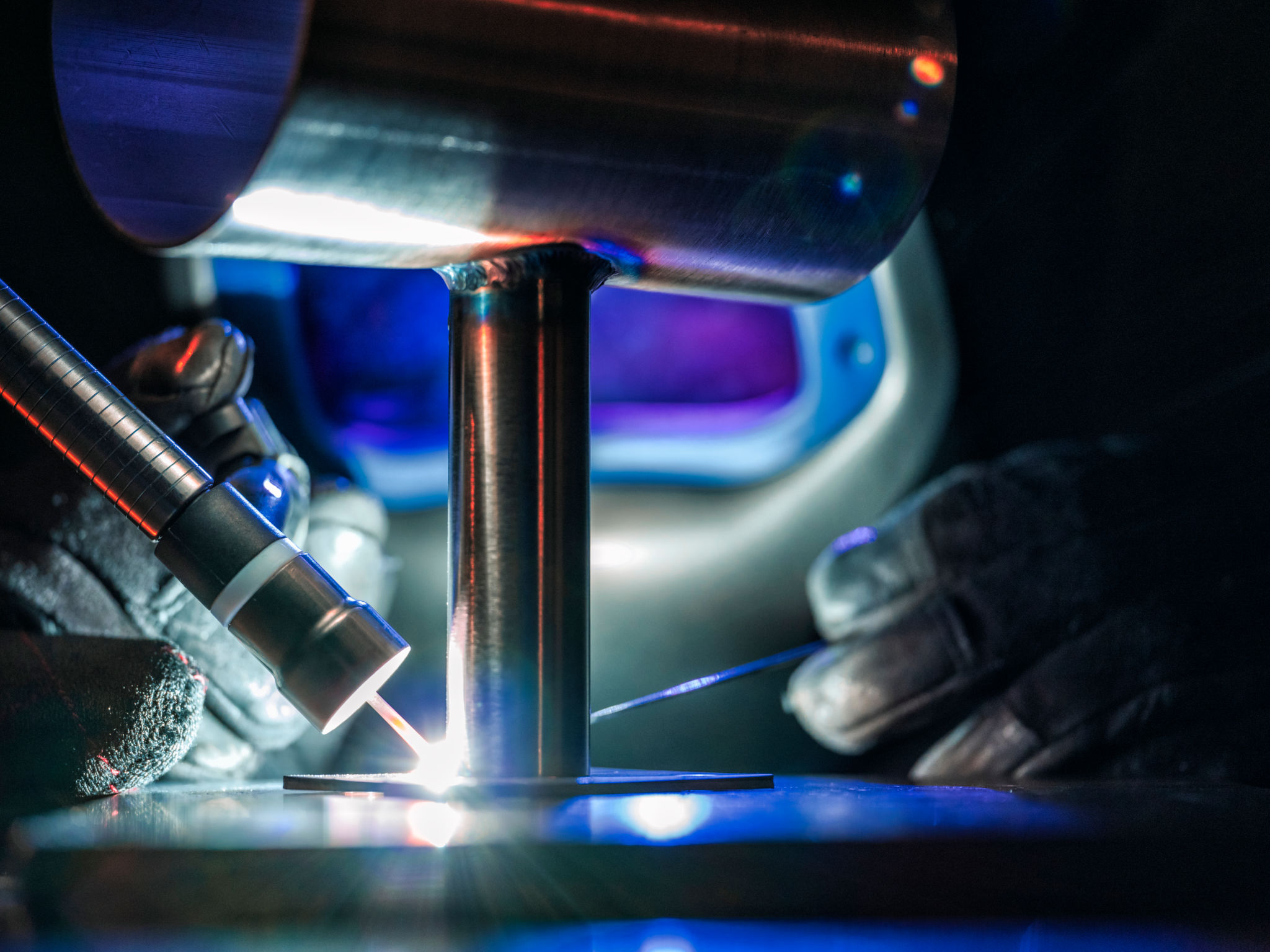
Enhanced Accuracy and Precision
One of the most significant benefits of digital tools in welding is the enhancement of accuracy and precision. Advanced software and digital interfaces allow welders to set parameters with unparalleled accuracy, ensuring that every weld meets exact specifications. This level of precision is essential in industries where even the smallest error can lead to significant issues.
Digital tools such as Computer-Aided Design (CAD) and Computer-Aided Manufacturing (CAM) have become indispensable in this transformation. They enable welders to plan and simulate welding processes with great accuracy, reducing the margin for error and improving overall output quality.
Efficiency Boost Through Automation
Automation is another area where digital tools are making a profound impact. Robotic welding systems, equipped with advanced sensors and AI-driven software, are increasingly being used to perform repetitive welding tasks. These systems not only speed up the welding process but also ensure consistent quality across large production runs.

Moreover, automated welding solutions reduce the need for human intervention in hazardous environments, significantly enhancing worker safety. This shift towards automation is a crucial step forward for companies looking to increase productivity while maintaining high safety standards.
Data-Driven Decision Making
Incorporating digital tools into welding processes also allows for data-driven decision-making. Welders can now collect, analyze, and interpret data from each weld to identify trends and areas for improvement. This data-driven approach helps in optimizing welding processes, reducing waste, and improving the overall efficiency of operations.
Advanced monitoring systems provide real-time feedback, allowing operators to adjust parameters on-the-fly to maintain quality and efficiency. This capability is particularly beneficial in dynamic environments where conditions can change rapidly.

Training and Skill Development
The introduction of digital tools has also transformed how welders are trained. Virtual reality (VR) and augmented reality (AR) simulations offer a safe and effective way for new welders to learn and practice their skills before applying them in real-world scenarios. These technologies provide immersive training experiences that enhance learning outcomes and reduce the time needed to become proficient.
Furthermore, digital training tools help experienced welders keep up with new techniques and technologies, ensuring that they remain competitive in an ever-evolving industry.
The Future of Welding in Springfield
The integration of digital tools into precision welding processes is just the beginning. As technology continues to advance, the potential for further innovations is immense. In Springfield, MO, businesses that embrace these advancements are likely to see significant benefits in terms of quality, efficiency, and competitiveness.
Industry leaders must stay informed about emerging technologies and be willing to invest in digital solutions that will drive their operations forward. By doing so, they can ensure they remain at the forefront of this rapidly changing industry.
Ultimately, the digital transformation of precision welding is an exciting development that promises to reshape the industry in Springfield and beyond. As companies continue to adopt these tools, the future looks bright for those willing to embrace change and innovation.